- Elkem
- Products
- Silicon based materials
- Silicon
What is silicon?
Elemental silicon (also known as silicon metal or metallurgical silicon) enables the manufacturing of a wide range of useful, efficient and sustainable products.
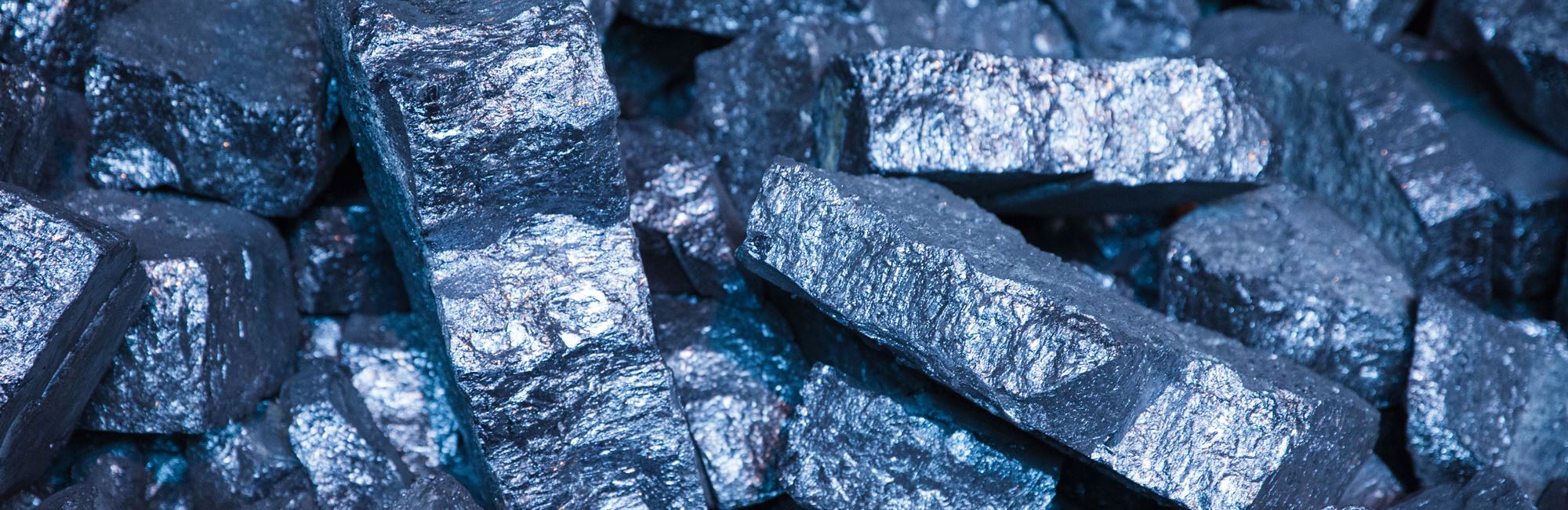
Silicon – Definition and how it is produced
As a chemical element, the silicon atom is referred to as the symbol 'Si', the atomic number 14 and has an atomic weight of 28. It is the second most abundant chemical element in the earth’s crust, just behind oxygen. Silicon metalloid, also referred to as a semi-metal or metal (although it isn’t one strictly speaking), is best known for its semiconductor characteristics and has been vital in the development of solar energy and electronics, driving digital technology. A semiconductor does not conduct electricity very well in its pure form but, by adding impurities, as is the case in silicon metalloids, it is possible to influence and control electron transport conductivity.
Silicon in its elemental form is not found in nature. It is present together with oxygen and other elements in various minerals. Silicon is typically produced from quartz or quartzite (SiO2), with low content of impurities. Unlike what many sources claim, silicon cannot be produced from fine, powder-like sand. The quartz used in the process is typically sized to 5–100 mm. To produce silicon, oxygen is combined with carbon to produce CO in a complex process with several reaction steps occurring at the same time in an electric arc furnace. The CO gas can be collected or reacted to CO2 when exposed to air.
Due to the high amount of gas produced in the process (CO and SiO), it is important to have a porous furnace charge that can ensure even distribution of the SiO gas in order to maximize the silicon yield. Therefore, it is a common practice to add significant amounts of wood chips to the furnace. This is also the reason why quartz sand cannot be used since it will clog the furnace. The SiO gas that is not captured in the furnace will escape and oxidize by air to silica fume (microsilica). The carbon used in the process can be sourced from biogenic sources, but all types of carbon sources can in principle be used. Elkem is putting a lot of effort into developing silicon, ferrosilicon and silicon metalloids with the lowest footprint possible, and the target in the climate roadmap is to reach net zero CO2 emissions in 2050. The process is also very energy-intensive, typically requiring about 10–14 MWh of electrical power to produce one metric tonne of silicon.
A unique aspect of Elkem’s operations is that we recover energy in most of our silicon furnaces, reducing the consumption of electrical power by about 30%.
Molten silicon is refined in a ladle to control the elements that are less noble than silicon (Al, Ca, etc.) and then cast into suitable molds. The elements that are more noble than silicon, like for instance iron, must be controlled with the composition of the raw materials. The solidified silicon is then crushed/milled to the required particle size.
Silicon – A raw material for the future
Commercially, the term 'silicon metal' is typically used for silicon that contains between 96% and 99.99% silicon. In the English language, 'silicon' and 'silicone' can easily be mixed up, and therefore the term 'silicon metal' is used even if this is not scientifically correct. The three main uses for silicon metal are:
- As an alloying element in aluminium production
- As the key raw material for the production of silicone, a polymer with countless applications
- For further processing to polysilicon, to obtain a purity level above 99.9999% for solar and electronic applications.
In addition, silicon metal is a key ingredient/raw material in a wide variety of products and applications such as:
- Fumed silica
- Refractory
- Ceramics
- Batteries
- Aluminum brazing
- Fillers
- Plasma spray
- Pyrotechnical applications
- Aluminum alloying.
We provides our customers with a wide range of silicon products featuring various purity and granularity characteristics that meet your specific needs. We work together with you to identify a suitable silicon solution for your application.
In all our activities, we assume our full responsibility as an industry leader to constantly develop the very best silicon products with a continuously lower environmental footprint, aiming to enable our customers to be competitive in their respective industries, whilst respecting the highest regulatory standards. This overriding goal is actively shared with our customers so that, together, we can manufacture environmentally and economically efficient products.
Contact us
Take your business to the next level by partnering with a world-leading material manufacturer.